Universal Testing Machine
Universal Hydraulic Tensile Test Machine (600/1000 kN capacity) is designed to test the ferrous materials for structural values such as yield strength and tensile strength. Apart from tensile tests, Universal Test Machines can also be used for compression tests up to the capacity of the machine and Bending Tests on 8-20 mm diameter rebars. Bending apparatus and mandrels for Bending tests and Ball Seating Assembly for compression tests should be ordered separately.
To Test Core samples up to 100 mm upper platen must be ordered separately.
Maximum security is maintained on 600kN/1000 kN capacity Universal Test Machine by limit switch on the lower grip as well as the safety check valves on the hydraulic system. Hydraulic power unit works silently.
0-40 mm flat and 8-32 mm round samples can be tested on 600 kN capacity frame and 0-40 mm flat and 8-40 mm round samples can be tested on 1000 kN capacity frame with a user friendly hydraulic jaws that comply with standards.
Load cell is used to measure stress. Strain measurement is done by the electronic displacement transducer built in the machine.
Tests can be done fully automatic by digital control unit or computer. Machine complete the test with the set pace rate and turns to start position automatically.
The distance between the grips can be set by motor driven hand set system. The system is controlled by a hand up/down system. With open front hydraulic wedge grips user can load specimen easily.
HYDRAULIC GRIPS
Hydraulically operated grips, completely stop the possibility of sample sliding from the grips enabling for correct and definite strain measurements. Hydraulic grips are very safe and user friendly. The hydraulic grips has an independent hydraulic power unit with a working pressure of 400 bars.
600 kN capacity Machine is supplied with 8-32 mm round samples grip set and 1000 kN capacity Machine is supplied with 8-40 mm round samples grip set.
Jaw faces for flat samples should be ordered separately.
BENDING APPARATUS
Bending Apparatus is used for Bending Tests on 8-20 mm diameter rebars.
Can be chosen HR-B6100 & HR-B1100 Models Tensile-Bending Testing Machine for Ø 8-40 mm rebars.
The test piece is bent over a mandrel.
The angle of bend and the diameter of the mandrel should be selected in accordance with the relevant product standard.
The bend test is performed with a minimum angle of bend of 180° over a mandrel according to TS 708 and TS EN 10080 Standards.
After the test, it is checked whether there are any visible breaks or cracks on the test pieces.
Bending apparatus and mandrels for bend tests should be ordered separately.
HYDRAULIC POWER PACK AND DIGITAL DATA ACQUISITION & CONTROL SYSTEM
Hydraulic Power Pack
Hydraulic Power Unit is designed to control the machine and processing of data from load-cell and displacement transducers which are fitted to the machine.
Controller unit has a simple and compact configuration.
Very silent power pack can load the specimen between 2mm/min - 18mm/min with an accuracy of ±5%. Safety valve (maximum pressure valve) is used to avoid machine overloading.
All the operations of Graphic Display are controlled from the front LCD display and function keys 2 analogue channels are provided for load-cells and displacement transducers.
It has easy to use menu options. It displays all menu option listings simultaneously, allowing the operator to access the required option in a seemless manner to activate the option or enter a numeric value to set the test parameters. The digital graphic display is able to draw stress vs. strain graph.
Dual Pumps
The dual pumps are formed by two groups;
One pump is controlled with digital readout unit with 3 phase controlled with and inverter to make test, other runs with a pedal to supply pressure to the grips. Grip pump has dual stage pump inside. On the dual stage pump, a high delivery, low pressure gear pump is used for rapid approach, for quick gripping the rebar while a low delivery, high pressure radial piston pump is used for 400 bar grip pressure.
Two Motors
The motor which drives the main pump in an AC motor and it is controlled by motor inverter. The variation in the oil flow is executed with the variation of the rotation speed of the motor.
The motor which drives the grip pump in an AC motor and it is controlled by a manual pedal. The maximum pressure of the grips can be monitored by a 0-600 bar manometer fitted to the end of the pipe of upper and lower grip connection.
Two Distribution Blocks
Two distribution blocks are used to control the oil flow direction supplied by the pumps, the following parts are fitted to the distribution block; Solenoid valve, Safety valve (max. pressure valve), Transducer and High pressure radial piston pump for main pump to make the test and Solenoid valve, Safety valve (max. pressure valve), low pressure gear pump and High pressure radial piston pump for grip pump.
Oil Tank
The tank includes enough oil to fill the mechanism which pushes the piston up during the test. The level and oil temperature can be seen on the indicator fitted to the tank. It has 60 L capacity. Hydraulic motor oil, number 46, must be used.
Digital Data Acquisition & Control System
The unit is designed to control the machine and processing of data from load-cells and displacement transducers which are fitted to the machine.
All the operations of the unit is controlled from the front panel consisting of a LCD display and function keys.
The unit has easy to use menu options.
Digital graphic display unit loading rate of the time of Testing and load values can be monitored.
Digital graphic display is able to draw real-time "Load vs. Time".
Software
Sample, company, laboratory and test values can be entered in the programme.
Stress-Strain, Load-time graphic, test reports and sample reports can be taken.
Software provides test data, results, and the Stress-Strain graphs can be seen at LCD screen.
The Universal Testing machine can be controlled (Start, Stop commands) by a computer with the software free of charge. This software provides data acquisition and management for compression, tensile and splitting tensile test throughout the test execution. The advanced functions for data base management provide an easy navigation of all saved data. The test results certificate includes all descriptive information. Therefore, test parameters can be set and details about the test carried out such as client details, test type, specimen type, user info and other information required can be entered and printed out as well as test report and graph.
Universal Test Software is developed for testing tensile strength of Reinforcing Rubbed Steel Bars and Welded fabric for the Reinforcement and Prestressing of Concrete. The software includes control of machine, data acquisition, saving them and preparing reports. The software accepts sample's weight, length, diameter and gauge length as input, and then the user can give start test command to the machine. The samples calculated diameter gives user a perspective about the density of rebar prior to the test. The software continuously updates load, stress and elongation percentage till the break point. The software is prepared as making at least 3 samples for each diameter. This gives user a total report about all the batch. The report includes all standard limits and one can easily check whether the sample can be acceptable. These limits are minimum yield, minimum tensile, minimum break elongation value, Tensile per yield ratio etc. Software can be performed in Turkish and English.
Test results, graphics and properties of 12 different specimens can be saved in one folder. Old test folders can be reviewed and be edited easily. Advanced Graphic User Interface Software.
User can highlight all 12 different specimen curves in different colors on the graphics.
Frequently used information like name and location of the laboratory, type and dimensions of mostly used specimens are held in memory and can be written automatically by right clicking on information boxes and selecting frequently used text in menu.
User can access any data of previously completed tests and use in his/ her new report since most of the tests have same structure and properties.
Main Features
To Test Core samples up to 100 mm upper platen must be ordered separately.
Maximum security is maintained on 600kN/1000 kN capacity Universal Test Machine by limit switch on the lower grip as well as the safety check valves on the hydraulic system. Hydraulic power unit works silently.
0-40 mm flat and 8-32 mm round samples can be tested on 600 kN capacity frame and 0-40 mm flat and 8-40 mm round samples can be tested on 1000 kN capacity frame with a user friendly hydraulic jaws that comply with standards.
Load cell is used to measure stress. Strain measurement is done by the electronic displacement transducer built in the machine.
Tests can be done fully automatic by digital control unit or computer. Machine complete the test with the set pace rate and turns to start position automatically.
The distance between the grips can be set by motor driven hand set system. The system is controlled by a hand up/down system. With open front hydraulic wedge grips user can load specimen easily.
HYDRAULIC GRIPS
Hydraulically operated grips, completely stop the possibility of sample sliding from the grips enabling for correct and definite strain measurements. Hydraulic grips are very safe and user friendly. The hydraulic grips has an independent hydraulic power unit with a working pressure of 400 bars.
600 kN capacity Machine is supplied with 8-32 mm round samples grip set and 1000 kN capacity Machine is supplied with 8-40 mm round samples grip set.
Jaw faces for flat samples should be ordered separately.
BENDING APPARATUS
Bending Apparatus is used for Bending Tests on 8-20 mm diameter rebars.
Can be chosen HR-B6100 & HR-B1100 Models Tensile-Bending Testing Machine for Ø 8-40 mm rebars.
The test piece is bent over a mandrel.
The angle of bend and the diameter of the mandrel should be selected in accordance with the relevant product standard.
The bend test is performed with a minimum angle of bend of 180° over a mandrel according to TS 708 and TS EN 10080 Standards.
After the test, it is checked whether there are any visible breaks or cracks on the test pieces.
Bending apparatus and mandrels for bend tests should be ordered separately.
HYDRAULIC POWER PACK AND DIGITAL DATA ACQUISITION & CONTROL SYSTEM
Hydraulic Power Pack
Hydraulic Power Unit is designed to control the machine and processing of data from load-cell and displacement transducers which are fitted to the machine.
Controller unit has a simple and compact configuration.
Very silent power pack can load the specimen between 2mm/min - 18mm/min with an accuracy of ±5%. Safety valve (maximum pressure valve) is used to avoid machine overloading.
All the operations of Graphic Display are controlled from the front LCD display and function keys 2 analogue channels are provided for load-cells and displacement transducers.
It has easy to use menu options. It displays all menu option listings simultaneously, allowing the operator to access the required option in a seemless manner to activate the option or enter a numeric value to set the test parameters. The digital graphic display is able to draw stress vs. strain graph.
Dual Pumps
The dual pumps are formed by two groups;
- Grip pump with dual stage pump
- Piston pump to make tensile and compression tests
One pump is controlled with digital readout unit with 3 phase controlled with and inverter to make test, other runs with a pedal to supply pressure to the grips. Grip pump has dual stage pump inside. On the dual stage pump, a high delivery, low pressure gear pump is used for rapid approach, for quick gripping the rebar while a low delivery, high pressure radial piston pump is used for 400 bar grip pressure.
Two Motors
The motor which drives the main pump in an AC motor and it is controlled by motor inverter. The variation in the oil flow is executed with the variation of the rotation speed of the motor.
The motor which drives the grip pump in an AC motor and it is controlled by a manual pedal. The maximum pressure of the grips can be monitored by a 0-600 bar manometer fitted to the end of the pipe of upper and lower grip connection.
Two Distribution Blocks
Two distribution blocks are used to control the oil flow direction supplied by the pumps, the following parts are fitted to the distribution block; Solenoid valve, Safety valve (max. pressure valve), Transducer and High pressure radial piston pump for main pump to make the test and Solenoid valve, Safety valve (max. pressure valve), low pressure gear pump and High pressure radial piston pump for grip pump.
Oil Tank
The tank includes enough oil to fill the mechanism which pushes the piston up during the test. The level and oil temperature can be seen on the indicator fitted to the tank. It has 60 L capacity. Hydraulic motor oil, number 46, must be used.
Digital Data Acquisition & Control System
The unit is designed to control the machine and processing of data from load-cells and displacement transducers which are fitted to the machine.
All the operations of the unit is controlled from the front panel consisting of a LCD display and function keys.
The unit has easy to use menu options.
Digital graphic display unit loading rate of the time of Testing and load values can be monitored.
Digital graphic display is able to draw real-time "Load vs. Time".
Software
Sample, company, laboratory and test values can be entered in the programme.
Stress-Strain, Load-time graphic, test reports and sample reports can be taken.
Software provides test data, results, and the Stress-Strain graphs can be seen at LCD screen.
The Universal Testing machine can be controlled (Start, Stop commands) by a computer with the software free of charge. This software provides data acquisition and management for compression, tensile and splitting tensile test throughout the test execution. The advanced functions for data base management provide an easy navigation of all saved data. The test results certificate includes all descriptive information. Therefore, test parameters can be set and details about the test carried out such as client details, test type, specimen type, user info and other information required can be entered and printed out as well as test report and graph.
Universal Test Software is developed for testing tensile strength of Reinforcing Rubbed Steel Bars and Welded fabric for the Reinforcement and Prestressing of Concrete. The software includes control of machine, data acquisition, saving them and preparing reports. The software accepts sample's weight, length, diameter and gauge length as input, and then the user can give start test command to the machine. The samples calculated diameter gives user a perspective about the density of rebar prior to the test. The software continuously updates load, stress and elongation percentage till the break point. The software is prepared as making at least 3 samples for each diameter. This gives user a total report about all the batch. The report includes all standard limits and one can easily check whether the sample can be acceptable. These limits are minimum yield, minimum tensile, minimum break elongation value, Tensile per yield ratio etc. Software can be performed in Turkish and English.
Test results, graphics and properties of 12 different specimens can be saved in one folder. Old test folders can be reviewed and be edited easily. Advanced Graphic User Interface Software.
User can highlight all 12 different specimen curves in different colors on the graphics.
Frequently used information like name and location of the laboratory, type and dimensions of mostly used specimens are held in memory and can be written automatically by right clicking on information boxes and selecting frequently used text in menu.
User can access any data of previously completed tests and use in his/ her new report since most of the tests have same structure and properties.
Main Features
- Can make test with displacement control.
- Real time display of test graph.
- 2 analog channels ( one for load cell, one for displacement transducer)
- 10 data per second sample rate for each channel
- Multi-language support (Turkish and English)
- 2 different unit system selection; SI and metric
- Real-time clock and date
- RS-232 serial port connection with the device
- Free of charge PC software for the test control and advanced report generation
EN ISO 15630-1, EN ISO 6892-1, EN ISO 7500-1, TS 708, TS EN 10080
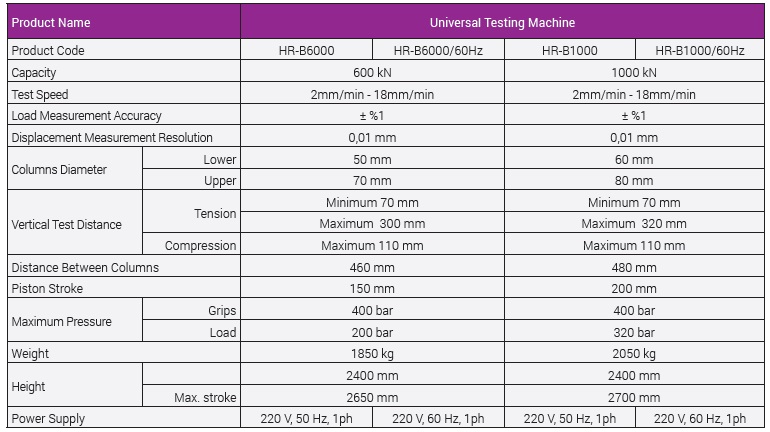
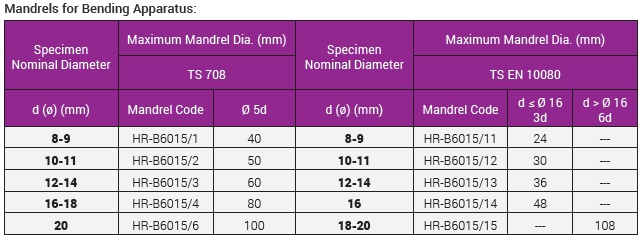
.jpg)